【乐虎集团的官方网站
】氯气nianxiangyuan
中间冷却器泄漏的原因有很多,涉及设备材质选择、设备加工、设备安装、工艺指标控制,特别是氯气含水量的控制及酸雾的控制、氯气中间冷却器的冷却介质即循环水的制备工艺等。本文将从氯气nianxiangyuan
氯气处理开始介绍,在整个氯气处理直至氯气压缩后输送过程中,各个过程安装及控制对氯气中冷器寿命可能造成影响的因素。氯气的洗涤、冷却、干燥、除雾、压缩过程统称为氯气处理,也会对氯气中冷器寿命造成影响。
1、氯气处理工艺流程简介
由离子膜电解槽出来的温度约为85-90℃的高温氯气,在电解工序通过钛列管式换热器与二次盐水工序的精制盐水进行换热,冷凝下来的氯水流至离子膜电解氯水罐,用氯水泵打入脱氯淡盐水塔进行真空脱氯。冷却后的氯气温度降温至50-55℃后汇总并入氯气主管线与氯酸盐分解,和淡盐水脱氯过来的氯气一起被送至氯气处理工序。
总体而言,在氯气处理工序氯气冷却采用一级洗涤加二级钛冷间接冷却相结合[1],硫酸干燥采用四塔串联干燥工艺,水雾和酸雾除雾器滤芯采用美国布林克除雾器滤芯,氯气nianxiangyuan
采用西门子KKK公司生产的透平离心式氯气nianxiangyuan
。该套氯气处理装置无论在电解初开车还是调峰生产变动负荷情况下,总体运行正常平稳,干燥氯气含水质量分数一直稳定在1*10-5以内,硫酸单耗稳定在12-14kg/t。
详细的处理过程为来自电解的氯气通过玻璃钢管道输送至氯气处理一级洗涤塔,塔内氯水由氯水泵加压经氯水冷却器冷却后,从洗涤塔塔顶喷淋头喷淋而下,与从下至上的高温氯气进行逆流接触,氯气降温至30℃进入钛列管式换热器,被7-9℃冷冻水间接冷却至12-16℃。在此过程中的所有氯水通过管道回流至氯气洗涤塔,通过洗涤塔泵出口的液位调节阀与洗涤塔液位自控联锁将氯水打至电解淡盐水脱氯工序回收利用。
从钛冷却器出来的氯气进入水雾捕集器除去水雾后,电解槽出来的氯气剩余含水量约降低为原来的1.6%[2],除雾后的氯气进入一级填料塔填料底部,填料塔循环硫酸通过硫酸磁力泵从塔底输送至硫酸板式换热器,通过7~9℃的冷冻水与硫酸换热后从塔顶硫酸分布器喷淋而下,在填料干燥塔中与氯气逆流接触,除去氯气中的水分。一级干燥塔至四级干燥塔的硫酸浓度依次约为75~78%、85~90%、93~95%、98%,硫酸控制的温度为14-15℃,氯气温度控制在14-15℃。其中在一级干燥塔的硫酸循环泵出口,设置一硫酸取样口、现场密度计及废酸控制调节阀,用于控制出酸。选择上述各塔出酸浓度有一定的原因,一般情况下,浓硫酸温度不应低于10℃,以防结晶,参见表1硫酸溶液的结晶温度表。

干燥后的氯气经过酸雾除雾器,除去硫酸雾和其它杂质后,进入氯气nianxiangyuan
压缩,经过四级压缩及四级氯气冷却器冷却,最终氯气被压缩至0.6-0.7MPaG,温度约为30-35℃,送至液化工序的原氯分配台。下图1为安邦公司氯气处理工序流程方框简图:
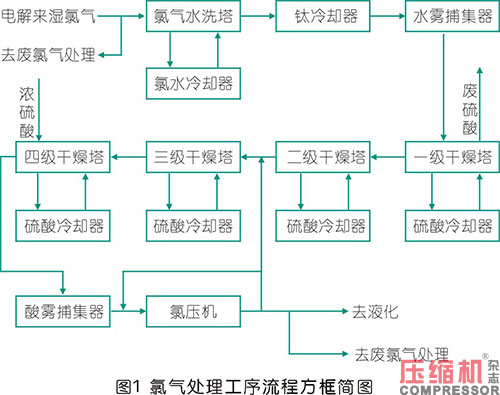
2、氯气处理装置运行情况
安邦公司氯气处理装置运行13年来,总体运行平稳,干燥氯气中含水完全达到了设计要求。在线水分分析仪显示一般保持在1*10-5以下,冬季水分可保持在0.5*10-5以下。由于电解调峰生产,调节较为频繁,2010年开机以来,硫酸消耗基本维持在12-14kg/t左右水平,近5年来年平均硫酸单耗在12.7、13.6、12.9、13.2、13.2kg/t。
氯气处理装置运行中各项工艺指标保持稳定,2022年5月16日各项工艺指标执行情况如下:
氯气洗涤塔氯气进口温度55.2℃
氯气洗涤塔氯气进口压力-0.45KPa
氯气洗涤塔氯气出口温度30.1℃
钛冷却器氯气出口温度13.45℃
一级干燥塔氯气出口温度14.2℃
一级干燥塔稀硫酸质量分数77.5%
二级干燥塔氯气出气温度14.3℃
二级干燥塔稀硫酸质量分数92%
三级干燥塔氯气出气温度14.1℃
三级干燥塔稀硫酸质量分数96%
四级干燥塔氯气出气温度14.2℃
四级干燥塔稀硫酸质量分数98%
氯气nianxiangyuan
进口氯气压力-12.8KPa
氯气nianxiangyuan
出口氯气温度32℃
氯气nianxiangyuan
出口氯气压力0.602MPa
氯气在线水分分析仪(I、IV级)0.56*10-5、0.62*10-5
3、氯气处理装置可能产生的问题及技术改进
3.1干燥塔填料故障,出塔水分增加,影响氯气中冷器寿命,可能造成腐蚀泄漏
氯气填料干燥塔内填料是有寿命的,正常情况下经过近4年的运行,原PVC填料逐步老化,会发生脆化变形现象。导致比表面积严重降低,氯气含水逐步上升,从原来稳定的5ppm左右,在约1个月时间内就可能上升至60ppm,且仍有继续上升趋势;干燥塔塔阻升高约2KPa,开始影响到氯压机的安全稳定运行。
氯气填料干燥塔水分开始逐步升高时,安邦公司在排除水分检测仪误差及故障、水雾捕集器故障原因后,初步怀疑PVC填料出现问题。
安邦公司氯气处理1级到4级干燥塔用的是PVC花环,73*27.5型,填料堆积密度是硫酸密度的4.3%,填料质量相对于硫酸质量可不计。
从当时硫酸用量、硫酸控制温度、氯气水份来判断,若水分检测仪结果为真,则出现该情况的原因最大的可能性为塔内填料发生软化降低,而且高度降低较多。硫酸用量增加及降低温度已起不到决定性作用。在氯气产量增加的情况下,氯气流速流量增加,硫酸用量虽然增加,但是接触面积不够导致水分无法及时吸附。
经过论证,安邦公司决定彻底更换四台塔内的PVC花环填料。对PVC花环和CPVC花环进行了温度耐受实验,PVC花环填料的耐受温度在65℃,60℃时强度开始降低;而CPVC耐受温度在85℃,80℃时强度未见明显降低,且据资料显示CPVC对腐蚀性介质比如氯气和浓硫酸的耐受性上有较为明显的优势,PVC花环在长期使用过程中会发生瘫软脆化甚至发生断裂,而CPVC花环填料相对PVC花环而言,CPVC尽管同样会发生强度的降低但不易发生变脆垮塌的风险。因此在确认CPVC花环填料的运行稳定性后,决定对每只塔更换填料体积为31.8396m3,比表面积127m2/m3,接触面积为4044m2。
安邦公司电解工序采用峰谷电调峰生产的方式,在电解A-D槽电流5kA,E-J槽电流6kA时,为低负荷;电解A-D槽电流11kA,E-J槽电流12.5kA时,为高负荷。PT0509为一级水洗塔前压力,PT0550为四级干燥塔出口压力,PT2450为酸雾捕集器出口压力,PT2451为氯压机进口压力,氯气处理阻力指水洗塔至酸雾捕集器出口之间的阻力,总阻力指水洗塔至氯压机进口包含氯压机进口过滤器的阻力。
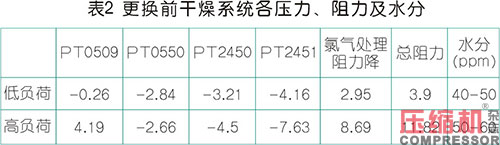
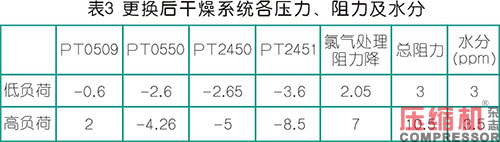
更换填料后,在同样高负荷情况下,电解氯气输送压力PT218压力从7.5kPa降至3.9kPa,降低3.6kPa;氯气处理总阻力降低1.3kPa,电解至氯压机进口管道总阻力降低4.9kPa。水分从60~90ppm降低至13ppm并仍然有下降趋势。
更换填料后电解系统至氯压机进口间的阻力降低效果明显,降低的4.9kPa压力可以提升电解槽A-D的电流约4kA,每小时多产3.3吨折百碱,每年多产2.67万吨折百碱。同时干燥系统的水分降低明显,保证了氯气nianxiangyuan
的安全稳定运行,同时有效防止了氯气中间冷却器因为水分含量高导致的腐蚀穿孔泄漏。
3.2氯气处理工艺指标控制值偏差导致水分升高,影响设备寿命
3.2.1.氯气处理的目的
从电解槽阳极析出的联产氯气温度很高,通常称之为“高温湿氯气”。湿氯气的化学性质要比干燥氯气更为强烈,几乎对钢铁以及绝大多数的金属有较强的腐蚀作用。只有少量的贵、稀金属或非金属材料在一定条件下,才能抵御此类氯气的腐蚀作用。因此给氯气的输送、使用、贮存等都带来了极大的麻烦和困难。而干燥后的氯气对钢铁等常用的金属材料的腐蚀作用在通常的条件之下是比较小的。详见氯中不同含水对钢铁的年腐蚀速率,见表4。

由上述腐蚀速率表可知,随着氯气中含水分的增加,每年的腐蚀速率也在增加。因此湿氯气的脱水和干燥是生产和使用氯气过程的需要。可见氯气处理的目的就是要除去湿氯气中的水分,使之成为含水分量甚微的干燥氯气以适应、满足氯气输送、生产、使用的需要。
3.2.2.氯气处理氯中含水与氯气温度控制的关系
从氯气处理的过程中,我们知道完整的氯气处理工艺应包括:“冷却除沫、干燥脱水、除雾净化、压缩输送和事故氯气处理”这五个部分。用通俗的话来讲就是:“先冷却、后干燥”工艺过程。
我们知道气体的“含湿量”与温度有着密切的关系。在不同的压力和温度下,气体中的“含湿量”(又称为“水蒸汽分压”)是不同的。饱和湿氯气中“含湿量”同样与温度有着密切的关系。一般来说,在压力相同的情况下,温度较高的气体中含水量要大于温度较低的气体。详见“氯气中含湿量与温度关系表5”:
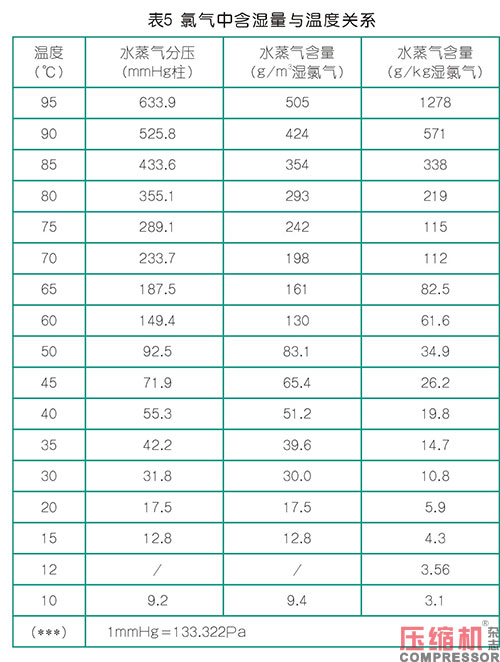
由表5可知,在相同的压力情况下,气体温度每下降10℃,湿氯气中的“含湿量”几乎降低近一半。若以电解槽阳极出口氯气温度为80℃的话,每千克湿氯气中所含的水分为219克。如果使用温度为30℃的工业上水将其冷却,使其温度降低至40℃;此时每千克湿氯气含水分为19.8克,可以通过冷却去除掉水分近200克,几乎去除掉91.3%的含水分。如果再用5~10℃的冷冻氯化钙盐水进一步冷却,让其温度降至12℃;则每千克湿氯气可去除水分16.24克。由此可见,湿氯气温度从80℃下降至12℃,每千克湿氯气可以去除掉水分215.44克,占98.4%。余下的1.6%水分进行干燥脱水,这样做是比较合理的。
按照降低气相的温度能够减少“含湿量”的观点,即气相的温度越低,气体中水蒸气分压也越低,所含水分也就越少。那么继续降低气相的温度,以求得较低的气体“含湿量”,这样的做法却是不可行、不可取的。原因是当氯气的温度降低到9.6℃时,将会形成Cl2·8H2O的结晶体,使冷凝下来的氯水结冰,将冷却器及其管道堵塞,使气体无法通过。因此湿氯气的温度不可无限制降低,应有适度,最佳的进干燥塔温度是12~16℃。
以上是通过冷却手段,使氯气中的含水分量减少了98.4%,这也就是实施“先冷却、后干燥”理论的效果。如果不采取冷却而直接用硫酸进行脱水干燥会是什么样子呢?我们用浓度为98%的硫酸干燥稀释至75%硫酸计的话,进行干燥脱水过程中,1吨硫酸吸收湿氯气中所含水分0.306吨。这样每干燥1吨湿氯气所消耗的98%硫酸为0.7吨。以年产20万吨100%烧碱生产能力计的话,每天处理600吨湿氯气需要消耗硫酸420吨。这样的消耗实在惊人。更令人吃惊的是:这些硫酸吸收了氯气中的水分所释放出来的稀释热量简直无法估量。以每千克浓硫酸吸收水分放出的溶解热为3557.675千焦(850千卡)计算,每天释放出的热量为1.49×109千焦。这些热量可将4462.5吨20℃水上升至100℃,这明显是不合理的。
3.2.3.氯气处理硫酸浓度控制对氯中含水的影响
在氯气洗涤降温除雾后,氯中含水的进一步降低需要通过浓硫酸干燥及除雾的方式进行脱除。
氯气在硫酸中的溶解度很小,可以说几乎不溶解于硫酸;而水分却能够以任意比例溶解于硫酸之中,从而组成不同浓度比例的硫酸溶液。因此在氯气处理工艺过程中“干燥脱水”这一步骤就借助于硫酸作溶剂;但是浓硫酸与湿氯气中的水分进行吸收传质的所谓“干燥脱水”,并不是在任何条件下都能实现的;而是需要一定的吸收传质条件,比如:温度、溶剂浓度等等。
要使吸收传质操作得以进行,需要解决三个问题:
a.选择合适的溶剂,要使其有选择性的溶解气相混合物中被分离的组分。在氯气处理工艺过程中,选择硫酸作为溶剂,它能够溶解氯气中被分离的组分水分,而对氯气却几乎不能溶解。
b.选择合适的吸收传质设备,以实现气液二相(溶质与溶剂)之间的接触,使被分离的组分能够从气相中转移到硫酸溶液中去。在氯气处理工艺过程中,选择了填料塔(泡沫塔、泡罩塔)等设备等,使气相中的溶质(水分)与液相的硫酸充分接触,使氯气中的水分能够转移到硫酸中去。
c.选择的溶剂能够循环使用。在氯气处理工艺过程中,溶剂硫酸能够在一定的浓度范围之内循环使用(98%~75%),并不断补充新溶剂,以确保溶剂有足够的循环量,使浓度不断地更新。
湿氯气中的所含水分处理量决定于硫酸液面上方的水蒸汽分压。而不同的浓度和温度的硫酸溶液的液面上方的水蒸汽分压力是不同的。把硫酸液面上的水蒸气分压力降低,就能提高硫酸吸收气相中所含水分进行传质的速率,也就能将“气相”湿氯气中所含水分量降到最低点。
那么,要降低硫酸液面上的水蒸气分压有两种途径:
a).在温度一定的状况下,溶剂硫酸的浓度越高,其液面上的水蒸气分压就越低(这是从参数浓度方面来考虑)。
b).在浓度一定的状况下,溶剂硫酸的温度降低,那么它的液面上水蒸汽分压随之下降,从而加大了传质吸收的过程的推动力。理解温度对硫酸吸水的影响请看示意图2。
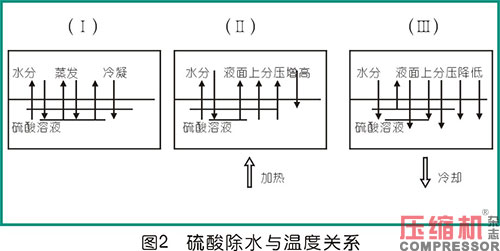
如图所示(Ⅰ)表示:硫酸溶液在一个封闭的容器中,溶液中的水分不断地从溶液中蒸发出来进入硫酸液面;几乎同时又有液面上的冷凝水蒸汽不断地进入硫酸溶液;因而,硫酸溶液的液面上水蒸气分压几乎不变,达到平衡状态。
如图所示(Ⅱ)表示:硫酸溶液在一个封闭的容器中,并且处于温度上升的加热状态,硫酸溶液中的水分大量的被蒸发出来进入硫酸溶液的液面;而液面上冷凝水蒸汽进入硫酸溶液几乎很少;因而造成硫酸液面上的水蒸汽分压增高,液面上的水蒸汽是很难进入硫酸溶液的。
如图所示(Ⅲ)表示:硫酸溶液在一个封闭的容器之中,并且处于温度下降的冷却状态,硫酸溶液中的水分由于温度降低而蒸发至液面上的很少,相反液面上的水蒸汽由于温度降低而大量的冷凝下来,进入溶液;因而造成硫酸液面上的水蒸气分压力降低,液面上的水蒸气是很容易进入硫酸溶液的。
当然,对于气相中含有双组分(氯气与水蒸汽)的混合物来说,其气相扩散组分(水蒸汽)扩散进入硫酸的过程,“费克定律”(Fickler principle)同样是适用的。即在单位时间之内,气相氯气中的扩散组分(水蒸汽)扩散通过单位面积的物质量是与扩散组分在扩散方向Z向上的浓度梯度成正比,因此降低硫酸浓度,可以降低硫酸表面水蒸气分压,更加有利于硫酸降低表面水蒸气分压从而在喷淋过程中增加传质推动力,促进氯气中的水分向冷硫酸中转移,达到脱除氯中含水的目的,保证氯气中间冷却器的安全,防止其产生泄漏。
在此说明一点,氯中含水水分一般控制在50ppm以内,控制的越低对设备而言越好。氯气nianxiangyuan
在运行时,会设置水分高报及停车指标,德国KKKnianxiangyuan
高报为240ppm,停车指标为480ppm。过高的水分不但对氯气中间冷却器造成腐蚀泄漏,同时也对氯气nianxiangyuan
的转子及管腔产生腐蚀。由于转子转速达到10000转/min,水分的失控危害极其严重,可在短期内造成转子的报废,导致转子压缩能力急剧下降,甚至造成转子不平衡导致导致事故的发生。曾有某厂家因氯中含水不达标导致氯气nianxiangyuan
一周内转子报废的事故发生。
3.3氯气nianxiangyuan
中间冷却器列管结垢造成堵塞导致局部产生腐蚀穿孔
原厂家提供的氯气中间冷却器图纸,采用八管程列管换热器,管道为Φ19*2碳钢管道。经过一年多的使用,发现该换热器存在冷却水折流管线过长,阻力大,导致水流速过缓,管道内部易杜塞、换热效果差,出口氯气温度逐步由原来的30℃升高至51℃。
针对原氯气中间冷却器,冷却水折流管线过长,阻力大,导致水流速过缓,管道内部易杜塞、换热效果差的问题,安邦公司进行了专门的分析和研究,制定了改进方案。
将氯气冷却器重新设计,将原八管程改为六管程,内部列管改为Φ25*3管道,排列方式为正三角排列,换热器循环水进出口管道由原来DN125改为DN150,因高位槽位置未变,进水压力保持不变,出口依然保持无压回水方式。
管道内水流方式为喘流,根据压差阻力与管径的关系,压差阻力反比于管径之比的5次方。改造后氯气中间冷却器的管程阻力降为改造前阻力的0.3倍,管内水流速增加,总传热系数大大增加。氯气温度由原来换热后51℃降低至25-30℃。改造后换热效果非常明显。
3.4氯气中间冷却器水侧暴露导致的电化腐蚀穿孔
氯气冷却器作为备件保存时应注意充氮气保存,将所有气相管口盲死确保密封,气相口用盲板盲死,在盲板上安装阀门及氮气进口。有必要时加装压力表,观察氯气冷却器气相压力泄漏情况。如果充入氮气后气相压力随着时间发生持续降低,应进行气密性试验。
氯气冷却器投入使用后,应注意气相压力高于冷却水压力,以防氯气冷却器水管泄漏时水进入气相,导致氯气nianxiangyuan
腐蚀造成更大事故。
氯气nianxiangyuan
岗位巡检人员在巡检时,每班次需打开水侧封头排气口将水中夹带的空气排尽,在每次开车加水时需打开排尽氯气冷却器内水中夹带的空气,而排水时同样需要打开排气口,以能够迅速从排污口排去氯气冷却器内水,防止氯气冷却器内水因排水导致空腔形成负压被吸住无法排尽。
在停车大修时,需要对氯气冷却器重点保护,除了氯气nianxiangyuan
需要通入高氮进行充气置换保护外,氯气冷却器水相也是重中之重。因水走的是管程,从氯气冷却器封头的底部进入,从上部无压溢出,碳钢设备充水容易在空气与水的接触面上发生锈蚀,要防止这个问题,有两种方法可以考虑。第一种是氯气冷却器管程保持充水满液状态后关闭进水阀门,为了保证气相压力大于水压力,需要调整氯气nianxiangyuan
进口的氮气阀门,保证氯气冷却器内气相压力超过水压力5kPa以上,以防止氯气冷却器泄漏水进入壳程。第二种方法是将氯气冷却器管程内水彻底排尽,排尽后从氯气冷却器E口充入氮气,从F口将水吹出,直至排水口无水喷出为止。
在做开车准备时,氯气冷却器充水前必须保证气相压力在15kPa以上,以时刻保证气相压力大于水压力。氯气冷却器充满水后,提高氯气nianxiangyuan
内氮气压力在25-40kPa之间,各项准备工作完毕后,开始启动氯气nianxiangyuan
。启动后,迅速调节进入氯气nianxiangyuan
的氮气阀门,保证氮气供应,防止氯气nianxiangyuan
启动后导致一级氯气nianxiangyuan
内气相压力为负值。氯气冷却器曾发生过两次因列管缺陷发生的泄漏,其中一次在氯气nianxiangyuan
启动后压力逐步上升的过程中,发生列管突然破裂,DCS氯气nianxiangyuan
冷却水PH值发生迅速下降,现场氯气报警仪出现氯气报警,迅速被发现后,系统停车处理,检测出具体的泄漏氯气冷却器,打开所有封头用水管对所有列管进行水置换,直至水清澈无异味,同理对封头及焊接面也必须彻底冲洗干净,防止氯水腐蚀。在整个过程中氯气nianxiangyuan
内始终充入大约200kPa的压力,用肥皂水进行试验,检查泄漏的列管,如果列管泄漏,干燥的氮气会将列管吹干,而不漏的列管保持潮湿状态,此时用肥皂水试验能够较快地发现泄漏的列管。整个过程如果处理迅速,可及时防止氯气冷却器的腐蚀,否则极易导致氯气冷却器被普遍腐蚀穿孔而报废,造成因处理不及时而产生更大的损失。需要注意的是检查出泄漏的列管后,堵焊后需要进行压力测试,进行打压试验至使用压力以上0.1MPa,稳压40分钟以上,24小时压力减小低于0.01MPa方可投入使用,以防砂眼无法查出导致进一步泄漏,并做好试压记录。
3.5氯气中冷器冷却循环水富氧化导致的泄漏
我公司氯气nianxiangyuan
中间冷却器及油冷却器循环水,采用独立的循环水冷却系统提供的循环水,与氯碱系统大循环水站独立。
主要原因为大循环水站水质由于浓缩倍数的关系,通常浓缩倍数≤3进行换水,经过在线检测PH大约在8-9,含盐量大约在0.8-1.0g/l,没有加药处理。氯碱系统换热设备的材质品种繁多,换热器数量较多,出现泄漏进入各种杂质离子的可能性增加,对氯气中冷器产生影响,造成腐蚀泄漏的可能性提高;大循环水站供水压力大约在0.5MPa,而氯气nianxiangyuan
中间冷却器的氯气压力从一级到四级依次大约为0.05MPa、0.15MPa、0.35MPa、0.65MPa,大循环水站供水压力由循环水泵供应,采用变频与出口温度调节,水压会发生变化,氯气中间冷却器采用手动阀门控制且要求气压必须大于水压,这给调节带来不稳定性。
为了确保水质的稳定性和供水压力的稳定性,我公司从第一套隔膜碱氯气nianxiangyuan
开始就设计采用独立的凉水塔系统,设计凉水塔冷水高位槽且设置回流至低位槽,水从12米高度的冷水高位槽内自然流到氯气中间冷却器及油冷却器内,水压稳定在0.12MPa。
原始采用河水作为补加水的方式,发现结垢较为严重,后改为纯水作为补加水,结垢问题得到彻底解决,但经过了解考证,单纯的纯水是不适宜独立作为补加水的。原因为碳钢中含有一定的碳,在纯水中,水与铁、碳形成原电池,纯水中的溶解氧、二氧化碳具有促进金属腐蚀的作用,即使在氧、二氧化碳浓度很低的情况下,也能引起严重的腐蚀。纯水对碳钢的腐蚀面积小、深;工业水对碳钢腐蚀的面积大、浅,容易使设备整体产生层状腐蚀[4]。由于点蚀的过程具有自催化的特征,从而促进腐蚀快速发展,这种腐蚀产生的穿孔特征为尖锐状针孔。在不完全密闭、不加处理剂的情况下,纯水对碳钢设备的腐蚀更不利于化工生产。要减少腐蚀,必须合理选择使用环境(如溴化锂冷水系统,完全密闭,不存在富氧化环境,纯水对碳钢设备腐蚀就可以忽略不计)。
如上所述,因敞开式凉水塔单纯加纯水对碳钢的腐蚀作用,我们采用的纯水为主,添加部分工业水,控制PH在7-8以上,电导率控制在<100us/cm,ORP控制在<300mv。经过实验,避免了工业水容易堵塞的问题,也解决了单纯纯水容易产生针孔腐蚀穿孔的问题。
4、结论
综上所述,氯气中间冷却器的使用安全,本质上也是保护主设备氯气nianxiangyuan
的使用安全。氯气nianxiangyuan
所涉及的辅助系统,如氯气处理干燥系统的工艺参数的运行质量、循环水站水质的控制及在线监测、设备材质选择及正确安装等都关系到氯气中间冷却器能否长周期安全稳定运行。
上述仅代表笔者本人的一点薄见,不妥之处,敬请同行业者批评指正。
参考文献
[1]王荣欣,肖娜.氯气干燥装置运行总结[J].氯碱工业,2014(10):25-26
[2]刘红民,周贤国,柴晔.降低氯中含水量的措施[J].中国氯碱,2008(7):6-7
[3]杨国稳.氯气处理工艺及关键点控制综述[J].中国氯碱,2016(10):11-14
[4]王建超,薛志清.工业水与纯水腐蚀碳钢的实验[J].氯碱工业,2015(3):44-45.
【乐虎集团的官方网站 】氯气nianxiangyuan 中间冷却器泄漏的原因有很多,涉及设备材质选择、设备加工、设备安装、工艺指标控制,特别是氯气含水量的控制及酸雾的控制、氯气中间冷却器的冷却介质即循环水的制备工艺等。本文将从氯气nianxiangyuan 氯气处理开始介绍,在整个氯气处理直至氯气压缩后输送过程中,各个过程安装及控制对氯气中冷器寿命可能造成影响的因素。氯气的洗涤、冷却、干燥、除雾、压缩过程统称为氯气处理,也会对氯气中冷器寿命造成影响。
1、氯气处理工艺流程简介
由离子膜电解槽出来的温度约为85-90℃的高温氯气,在电解工序通过钛列管式换热器与二次盐水工序的精制盐水进行换热,冷凝下来的氯水流至离子膜电解氯水罐,用氯水泵打入脱氯淡盐水塔进行真空脱氯。冷却后的氯气温度降温至50-55℃后汇总并入氯气主管线与氯酸盐分解,和淡盐水脱氯过来的氯气一起被送至氯气处理工序。
总体而言,在氯气处理工序氯气冷却采用一级洗涤加二级钛冷间接冷却相结合[1],硫酸干燥采用四塔串联干燥工艺,水雾和酸雾除雾器滤芯采用美国布林克除雾器滤芯,氯气nianxiangyuan 采用西门子KKK公司生产的透平离心式氯气nianxiangyuan 。该套氯气处理装置无论在电解初开车还是调峰生产变动负荷情况下,总体运行正常平稳,干燥氯气含水质量分数一直稳定在1*10-5以内,硫酸单耗稳定在12-14kg/t。
详细的处理过程为来自电解的氯气通过玻璃钢管道输送至氯气处理一级洗涤塔,塔内氯水由氯水泵加压经氯水冷却器冷却后,从洗涤塔塔顶喷淋头喷淋而下,与从下至上的高温氯气进行逆流接触,氯气降温至30℃进入钛列管式换热器,被7-9℃冷冻水间接冷却至12-16℃。在此过程中的所有氯水通过管道回流至氯气洗涤塔,通过洗涤塔泵出口的液位调节阀与洗涤塔液位自控联锁将氯水打至电解淡盐水脱氯工序回收利用。
从钛冷却器出来的氯气进入水雾捕集器除去水雾后,电解槽出来的氯气剩余含水量约降低为原来的1.6%[2],除雾后的氯气进入一级填料塔填料底部,填料塔循环硫酸通过硫酸磁力泵从塔底输送至硫酸板式换热器,通过7~9℃的冷冻水与硫酸换热后从塔顶硫酸分布器喷淋而下,在填料干燥塔中与氯气逆流接触,除去氯气中的水分。一级干燥塔至四级干燥塔的硫酸浓度依次约为75~78%、85~90%、93~95%、98%,硫酸控制的温度为14-15℃,氯气温度控制在14-15℃。其中在一级干燥塔的硫酸循环泵出口,设置一硫酸取样口、现场密度计及废酸控制调节阀,用于控制出酸。选择上述各塔出酸浓度有一定的原因,一般情况下,浓硫酸温度不应低于10℃,以防结晶,参见表1硫酸溶液的结晶温度表。
干燥后的氯气经过酸雾除雾器,除去硫酸雾和其它杂质后,进入氯气nianxiangyuan 压缩,经过四级压缩及四级氯气冷却器冷却,最终氯气被压缩至0.6-0.7MPaG,温度约为30-35℃,送至液化工序的原氯分配台。下图1为安邦公司氯气处理工序流程方框简图:
2、氯气处理装置运行情况
安邦公司氯气处理装置运行13年来,总体运行平稳,干燥氯气中含水完全达到了设计要求。在线水分分析仪显示一般保持在1*10-5以下,冬季水分可保持在0.5*10-5以下。由于电解调峰生产,调节较为频繁,2010年开机以来,硫酸消耗基本维持在12-14kg/t左右水平,近5年来年平均硫酸单耗在12.7、13.6、12.9、13.2、13.2kg/t。
氯气处理装置运行中各项工艺指标保持稳定,2022年5月16日各项工艺指标执行情况如下:
氯气洗涤塔氯气进口温度55.2℃
氯气洗涤塔氯气进口压力-0.45KPa
氯气洗涤塔氯气出口温度30.1℃
钛冷却器氯气出口温度13.45℃
一级干燥塔氯气出口温度14.2℃
一级干燥塔稀硫酸质量分数77.5%
二级干燥塔氯气出气温度14.3℃
二级干燥塔稀硫酸质量分数92%
三级干燥塔氯气出气温度14.1℃
三级干燥塔稀硫酸质量分数96%
四级干燥塔氯气出气温度14.2℃
四级干燥塔稀硫酸质量分数98%
氯气nianxiangyuan 进口氯气压力-12.8KPa
氯气nianxiangyuan 出口氯气温度32℃
氯气nianxiangyuan 出口氯气压力0.602MPa
氯气在线水分分析仪(I、IV级)0.56*10-5、0.62*10-5
3、氯气处理装置可能产生的问题及技术改进
3.1干燥塔填料故障,出塔水分增加,影响氯气中冷器寿命,可能造成腐蚀泄漏
氯气填料干燥塔内填料是有寿命的,正常情况下经过近4年的运行,原PVC填料逐步老化,会发生脆化变形现象。导致比表面积严重降低,氯气含水逐步上升,从原来稳定的5ppm左右,在约1个月时间内就可能上升至60ppm,且仍有继续上升趋势;干燥塔塔阻升高约2KPa,开始影响到氯压机的安全稳定运行。
氯气填料干燥塔水分开始逐步升高时,安邦公司在排除水分检测仪误差及故障、水雾捕集器故障原因后,初步怀疑PVC填料出现问题。
安邦公司氯气处理1级到4级干燥塔用的是PVC花环,73*27.5型,填料堆积密度是硫酸密度的4.3%,填料质量相对于硫酸质量可不计。
从当时硫酸用量、硫酸控制温度、氯气水份来判断,若水分检测仪结果为真,则出现该情况的原因最大的可能性为塔内填料发生软化降低,而且高度降低较多。硫酸用量增加及降低温度已起不到决定性作用。在氯气产量增加的情况下,氯气流速流量增加,硫酸用量虽然增加,但是接触面积不够导致水分无法及时吸附。
经过论证,安邦公司决定彻底更换四台塔内的PVC花环填料。对PVC花环和CPVC花环进行了温度耐受实验,PVC花环填料的耐受温度在65℃,60℃时强度开始降低;而CPVC耐受温度在85℃,80℃时强度未见明显降低,且据资料显示CPVC对腐蚀性介质比如氯气和浓硫酸的耐受性上有较为明显的优势,PVC花环在长期使用过程中会发生瘫软脆化甚至发生断裂,而CPVC花环填料相对PVC花环而言,CPVC尽管同样会发生强度的降低但不易发生变脆垮塌的风险。因此在确认CPVC花环填料的运行稳定性后,决定对每只塔更换填料体积为31.8396m3,比表面积127m2/m3,接触面积为4044m2。
安邦公司电解工序采用峰谷电调峰生产的方式,在电解A-D槽电流5kA,E-J槽电流6kA时,为低负荷;电解A-D槽电流11kA,E-J槽电流12.5kA时,为高负荷。PT0509为一级水洗塔前压力,PT0550为四级干燥塔出口压力,PT2450为酸雾捕集器出口压力,PT2451为氯压机进口压力,氯气处理阻力指水洗塔至酸雾捕集器出口之间的阻力,总阻力指水洗塔至氯压机进口包含氯压机进口过滤器的阻力。
更换填料后,在同样高负荷情况下,电解氯气输送压力PT218压力从7.5kPa降至3.9kPa,降低3.6kPa;氯气处理总阻力降低1.3kPa,电解至氯压机进口管道总阻力降低4.9kPa。水分从60~90ppm降低至13ppm并仍然有下降趋势。
更换填料后电解系统至氯压机进口间的阻力降低效果明显,降低的4.9kPa压力可以提升电解槽A-D的电流约4kA,每小时多产3.3吨折百碱,每年多产2.67万吨折百碱。同时干燥系统的水分降低明显,保证了氯气nianxiangyuan 的安全稳定运行,同时有效防止了氯气中间冷却器因为水分含量高导致的腐蚀穿孔泄漏。
3.2氯气处理工艺指标控制值偏差导致水分升高,影响设备寿命
3.2.1.氯气处理的目的
从电解槽阳极析出的联产氯气温度很高,通常称之为“高温湿氯气”。湿氯气的化学性质要比干燥氯气更为强烈,几乎对钢铁以及绝大多数的金属有较强的腐蚀作用。只有少量的贵、稀金属或非金属材料在一定条件下,才能抵御此类氯气的腐蚀作用。因此给氯气的输送、使用、贮存等都带来了极大的麻烦和困难。而干燥后的氯气对钢铁等常用的金属材料的腐蚀作用在通常的条件之下是比较小的。详见氯中不同含水对钢铁的年腐蚀速率,见表4。
由上述腐蚀速率表可知,随着氯气中含水分的增加,每年的腐蚀速率也在增加。因此湿氯气的脱水和干燥是生产和使用氯气过程的需要。可见氯气处理的目的就是要除去湿氯气中的水分,使之成为含水分量甚微的干燥氯气以适应、满足氯气输送、生产、使用的需要。
3.2.2.氯气处理氯中含水与氯气温度控制的关系
从氯气处理的过程中,我们知道完整的氯气处理工艺应包括:“冷却除沫、干燥脱水、除雾净化、压缩输送和事故氯气处理”这五个部分。用通俗的话来讲就是:“先冷却、后干燥”工艺过程。
我们知道气体的“含湿量”与温度有着密切的关系。在不同的压力和温度下,气体中的“含湿量”(又称为“水蒸汽分压”)是不同的。饱和湿氯气中“含湿量”同样与温度有着密切的关系。一般来说,在压力相同的情况下,温度较高的气体中含水量要大于温度较低的气体。详见“氯气中含湿量与温度关系表5”:
由表5可知,在相同的压力情况下,气体温度每下降10℃,湿氯气中的“含湿量”几乎降低近一半。若以电解槽阳极出口氯气温度为80℃的话,每千克湿氯气中所含的水分为219克。如果使用温度为30℃的工业上水将其冷却,使其温度降低至40℃;此时每千克湿氯气含水分为19.8克,可以通过冷却去除掉水分近200克,几乎去除掉91.3%的含水分。如果再用5~10℃的冷冻氯化钙盐水进一步冷却,让其温度降至12℃;则每千克湿氯气可去除水分16.24克。由此可见,湿氯气温度从80℃下降至12℃,每千克湿氯气可以去除掉水分215.44克,占98.4%。余下的1.6%水分进行干燥脱水,这样做是比较合理的。
按照降低气相的温度能够减少“含湿量”的观点,即气相的温度越低,气体中水蒸气分压也越低,所含水分也就越少。那么继续降低气相的温度,以求得较低的气体“含湿量”,这样的做法却是不可行、不可取的。原因是当氯气的温度降低到9.6℃时,将会形成Cl2·8H2O的结晶体,使冷凝下来的氯水结冰,将冷却器及其管道堵塞,使气体无法通过。因此湿氯气的温度不可无限制降低,应有适度,最佳的进干燥塔温度是12~16℃。
以上是通过冷却手段,使氯气中的含水分量减少了98.4%,这也就是实施“先冷却、后干燥”理论的效果。如果不采取冷却而直接用硫酸进行脱水干燥会是什么样子呢?我们用浓度为98%的硫酸干燥稀释至75%硫酸计的话,进行干燥脱水过程中,1吨硫酸吸收湿氯气中所含水分0.306吨。这样每干燥1吨湿氯气所消耗的98%硫酸为0.7吨。以年产20万吨100%烧碱生产能力计的话,每天处理600吨湿氯气需要消耗硫酸420吨。这样的消耗实在惊人。更令人吃惊的是:这些硫酸吸收了氯气中的水分所释放出来的稀释热量简直无法估量。以每千克浓硫酸吸收水分放出的溶解热为3557.675千焦(850千卡)计算,每天释放出的热量为1.49×109千焦。这些热量可将4462.5吨20℃水上升至100℃,这明显是不合理的。
3.2.3.氯气处理硫酸浓度控制对氯中含水的影响
在氯气洗涤降温除雾后,氯中含水的进一步降低需要通过浓硫酸干燥及除雾的方式进行脱除。
氯气在硫酸中的溶解度很小,可以说几乎不溶解于硫酸;而水分却能够以任意比例溶解于硫酸之中,从而组成不同浓度比例的硫酸溶液。因此在氯气处理工艺过程中“干燥脱水”这一步骤就借助于硫酸作溶剂;但是浓硫酸与湿氯气中的水分进行吸收传质的所谓“干燥脱水”,并不是在任何条件下都能实现的;而是需要一定的吸收传质条件,比如:温度、溶剂浓度等等。
要使吸收传质操作得以进行,需要解决三个问题:
a.选择合适的溶剂,要使其有选择性的溶解气相混合物中被分离的组分。在氯气处理工艺过程中,选择硫酸作为溶剂,它能够溶解氯气中被分离的组分水分,而对氯气却几乎不能溶解。
b.选择合适的吸收传质设备,以实现气液二相(溶质与溶剂)之间的接触,使被分离的组分能够从气相中转移到硫酸溶液中去。在氯气处理工艺过程中,选择了填料塔(泡沫塔、泡罩塔)等设备等,使气相中的溶质(水分)与液相的硫酸充分接触,使氯气中的水分能够转移到硫酸中去。
c.选择的溶剂能够循环使用。在氯气处理工艺过程中,溶剂硫酸能够在一定的浓度范围之内循环使用(98%~75%),并不断补充新溶剂,以确保溶剂有足够的循环量,使浓度不断地更新。
湿氯气中的所含水分处理量决定于硫酸液面上方的水蒸汽分压。而不同的浓度和温度的硫酸溶液的液面上方的水蒸汽分压力是不同的。把硫酸液面上的水蒸气分压力降低,就能提高硫酸吸收气相中所含水分进行传质的速率,也就能将“气相”湿氯气中所含水分量降到最低点。
那么,要降低硫酸液面上的水蒸气分压有两种途径:
a).在温度一定的状况下,溶剂硫酸的浓度越高,其液面上的水蒸气分压就越低(这是从参数浓度方面来考虑)。
b).在浓度一定的状况下,溶剂硫酸的温度降低,那么它的液面上水蒸汽分压随之下降,从而加大了传质吸收的过程的推动力。理解温度对硫酸吸水的影响请看示意图2。
如图所示(Ⅰ)表示:硫酸溶液在一个封闭的容器中,溶液中的水分不断地从溶液中蒸发出来进入硫酸液面;几乎同时又有液面上的冷凝水蒸汽不断地进入硫酸溶液;因而,硫酸溶液的液面上水蒸气分压几乎不变,达到平衡状态。
如图所示(Ⅱ)表示:硫酸溶液在一个封闭的容器中,并且处于温度上升的加热状态,硫酸溶液中的水分大量的被蒸发出来进入硫酸溶液的液面;而液面上冷凝水蒸汽进入硫酸溶液几乎很少;因而造成硫酸液面上的水蒸汽分压增高,液面上的水蒸汽是很难进入硫酸溶液的。
如图所示(Ⅲ)表示:硫酸溶液在一个封闭的容器之中,并且处于温度下降的冷却状态,硫酸溶液中的水分由于温度降低而蒸发至液面上的很少,相反液面上的水蒸汽由于温度降低而大量的冷凝下来,进入溶液;因而造成硫酸液面上的水蒸气分压力降低,液面上的水蒸气是很容易进入硫酸溶液的。
当然,对于气相中含有双组分(氯气与水蒸汽)的混合物来说,其气相扩散组分(水蒸汽)扩散进入硫酸的过程,“费克定律”(Fickler principle)同样是适用的。即在单位时间之内,气相氯气中的扩散组分(水蒸汽)扩散通过单位面积的物质量是与扩散组分在扩散方向Z向上的浓度梯度成正比,因此降低硫酸浓度,可以降低硫酸表面水蒸气分压,更加有利于硫酸降低表面水蒸气分压从而在喷淋过程中增加传质推动力,促进氯气中的水分向冷硫酸中转移,达到脱除氯中含水的目的,保证氯气中间冷却器的安全,防止其产生泄漏。
在此说明一点,氯中含水水分一般控制在50ppm以内,控制的越低对设备而言越好。氯气nianxiangyuan 在运行时,会设置水分高报及停车指标,德国KKKnianxiangyuan 高报为240ppm,停车指标为480ppm。过高的水分不但对氯气中间冷却器造成腐蚀泄漏,同时也对氯气nianxiangyuan 的转子及管腔产生腐蚀。由于转子转速达到10000转/min,水分的失控危害极其严重,可在短期内造成转子的报废,导致转子压缩能力急剧下降,甚至造成转子不平衡导致导致事故的发生。曾有某厂家因氯中含水不达标导致氯气nianxiangyuan 一周内转子报废的事故发生。
3.3氯气nianxiangyuan 中间冷却器列管结垢造成堵塞导致局部产生腐蚀穿孔
原厂家提供的氯气中间冷却器图纸,采用八管程列管换热器,管道为Φ19*2碳钢管道。经过一年多的使用,发现该换热器存在冷却水折流管线过长,阻力大,导致水流速过缓,管道内部易杜塞、换热效果差,出口氯气温度逐步由原来的30℃升高至51℃。
针对原氯气中间冷却器,冷却水折流管线过长,阻力大,导致水流速过缓,管道内部易杜塞、换热效果差的问题,安邦公司进行了专门的分析和研究,制定了改进方案。
将氯气冷却器重新设计,将原八管程改为六管程,内部列管改为Φ25*3管道,排列方式为正三角排列,换热器循环水进出口管道由原来DN125改为DN150,因高位槽位置未变,进水压力保持不变,出口依然保持无压回水方式。
管道内水流方式为喘流,根据压差阻力与管径的关系,压差阻力反比于管径之比的5次方。改造后氯气中间冷却器的管程阻力降为改造前阻力的0.3倍,管内水流速增加,总传热系数大大增加。氯气温度由原来换热后51℃降低至25-30℃。改造后换热效果非常明显。
3.4氯气中间冷却器水侧暴露导致的电化腐蚀穿孔
氯气冷却器作为备件保存时应注意充氮气保存,将所有气相管口盲死确保密封,气相口用盲板盲死,在盲板上安装阀门及氮气进口。有必要时加装压力表,观察氯气冷却器气相压力泄漏情况。如果充入氮气后气相压力随着时间发生持续降低,应进行气密性试验。
氯气冷却器投入使用后,应注意气相压力高于冷却水压力,以防氯气冷却器水管泄漏时水进入气相,导致氯气nianxiangyuan 腐蚀造成更大事故。
氯气nianxiangyuan 岗位巡检人员在巡检时,每班次需打开水侧封头排气口将水中夹带的空气排尽,在每次开车加水时需打开排尽氯气冷却器内水中夹带的空气,而排水时同样需要打开排气口,以能够迅速从排污口排去氯气冷却器内水,防止氯气冷却器内水因排水导致空腔形成负压被吸住无法排尽。
在停车大修时,需要对氯气冷却器重点保护,除了氯气nianxiangyuan 需要通入高氮进行充气置换保护外,氯气冷却器水相也是重中之重。因水走的是管程,从氯气冷却器封头的底部进入,从上部无压溢出,碳钢设备充水容易在空气与水的接触面上发生锈蚀,要防止这个问题,有两种方法可以考虑。第一种是氯气冷却器管程保持充水满液状态后关闭进水阀门,为了保证气相压力大于水压力,需要调整氯气nianxiangyuan 进口的氮气阀门,保证氯气冷却器内气相压力超过水压力5kPa以上,以防止氯气冷却器泄漏水进入壳程。第二种方法是将氯气冷却器管程内水彻底排尽,排尽后从氯气冷却器E口充入氮气,从F口将水吹出,直至排水口无水喷出为止。
在做开车准备时,氯气冷却器充水前必须保证气相压力在15kPa以上,以时刻保证气相压力大于水压力。氯气冷却器充满水后,提高氯气nianxiangyuan 内氮气压力在25-40kPa之间,各项准备工作完毕后,开始启动氯气nianxiangyuan 。启动后,迅速调节进入氯气nianxiangyuan 的氮气阀门,保证氮气供应,防止氯气nianxiangyuan 启动后导致一级氯气nianxiangyuan 内气相压力为负值。氯气冷却器曾发生过两次因列管缺陷发生的泄漏,其中一次在氯气nianxiangyuan 启动后压力逐步上升的过程中,发生列管突然破裂,DCS氯气nianxiangyuan 冷却水PH值发生迅速下降,现场氯气报警仪出现氯气报警,迅速被发现后,系统停车处理,检测出具体的泄漏氯气冷却器,打开所有封头用水管对所有列管进行水置换,直至水清澈无异味,同理对封头及焊接面也必须彻底冲洗干净,防止氯水腐蚀。在整个过程中氯气nianxiangyuan 内始终充入大约200kPa的压力,用肥皂水进行试验,检查泄漏的列管,如果列管泄漏,干燥的氮气会将列管吹干,而不漏的列管保持潮湿状态,此时用肥皂水试验能够较快地发现泄漏的列管。整个过程如果处理迅速,可及时防止氯气冷却器的腐蚀,否则极易导致氯气冷却器被普遍腐蚀穿孔而报废,造成因处理不及时而产生更大的损失。需要注意的是检查出泄漏的列管后,堵焊后需要进行压力测试,进行打压试验至使用压力以上0.1MPa,稳压40分钟以上,24小时压力减小低于0.01MPa方可投入使用,以防砂眼无法查出导致进一步泄漏,并做好试压记录。
3.5氯气中冷器冷却循环水富氧化导致的泄漏
我公司氯气nianxiangyuan 中间冷却器及油冷却器循环水,采用独立的循环水冷却系统提供的循环水,与氯碱系统大循环水站独立。
主要原因为大循环水站水质由于浓缩倍数的关系,通常浓缩倍数≤3进行换水,经过在线检测PH大约在8-9,含盐量大约在0.8-1.0g/l,没有加药处理。氯碱系统换热设备的材质品种繁多,换热器数量较多,出现泄漏进入各种杂质离子的可能性增加,对氯气中冷器产生影响,造成腐蚀泄漏的可能性提高;大循环水站供水压力大约在0.5MPa,而氯气nianxiangyuan 中间冷却器的氯气压力从一级到四级依次大约为0.05MPa、0.15MPa、0.35MPa、0.65MPa,大循环水站供水压力由循环水泵供应,采用变频与出口温度调节,水压会发生变化,氯气中间冷却器采用手动阀门控制且要求气压必须大于水压,这给调节带来不稳定性。
为了确保水质的稳定性和供水压力的稳定性,我公司从第一套隔膜碱氯气nianxiangyuan 开始就设计采用独立的凉水塔系统,设计凉水塔冷水高位槽且设置回流至低位槽,水从12米高度的冷水高位槽内自然流到氯气中间冷却器及油冷却器内,水压稳定在0.12MPa。
原始采用河水作为补加水的方式,发现结垢较为严重,后改为纯水作为补加水,结垢问题得到彻底解决,但经过了解考证,单纯的纯水是不适宜独立作为补加水的。原因为碳钢中含有一定的碳,在纯水中,水与铁、碳形成原电池,纯水中的溶解氧、二氧化碳具有促进金属腐蚀的作用,即使在氧、二氧化碳浓度很低的情况下,也能引起严重的腐蚀。纯水对碳钢的腐蚀面积小、深;工业水对碳钢腐蚀的面积大、浅,容易使设备整体产生层状腐蚀[4]。由于点蚀的过程具有自催化的特征,从而促进腐蚀快速发展,这种腐蚀产生的穿孔特征为尖锐状针孔。在不完全密闭、不加处理剂的情况下,纯水对碳钢设备的腐蚀更不利于化工生产。要减少腐蚀,必须合理选择使用环境(如溴化锂冷水系统,完全密闭,不存在富氧化环境,纯水对碳钢设备腐蚀就可以忽略不计)。
如上所述,因敞开式凉水塔单纯加纯水对碳钢的腐蚀作用,我们采用的纯水为主,添加部分工业水,控制PH在7-8以上,电导率控制在<100us/cm,ORP控制在<300mv。经过实验,避免了工业水容易堵塞的问题,也解决了单纯纯水容易产生针孔腐蚀穿孔的问题。
4、结论
综上所述,氯气中间冷却器的使用安全,本质上也是保护主设备氯气nianxiangyuan 的使用安全。氯气nianxiangyuan 所涉及的辅助系统,如氯气处理干燥系统的工艺参数的运行质量、循环水站水质的控制及在线监测、设备材质选择及正确安装等都关系到氯气中间冷却器能否长周期安全稳定运行。
上述仅代表笔者本人的一点薄见,不妥之处,敬请同行业者批评指正。
参考文献
[1]王荣欣,肖娜.氯气干燥装置运行总结[J].氯碱工业,2014(10):25-26
[2]刘红民,周贤国,柴晔.降低氯中含水量的措施[J].中国氯碱,2008(7):6-7
[3]杨国稳.氯气处理工艺及关键点控制综述[J].中国氯碱,2016(10):11-14
[4]王建超,薛志清.工业水与纯水腐蚀碳钢的实验[J].氯碱工业,2015(3):44-45.
网友评论
条评论
最新评论